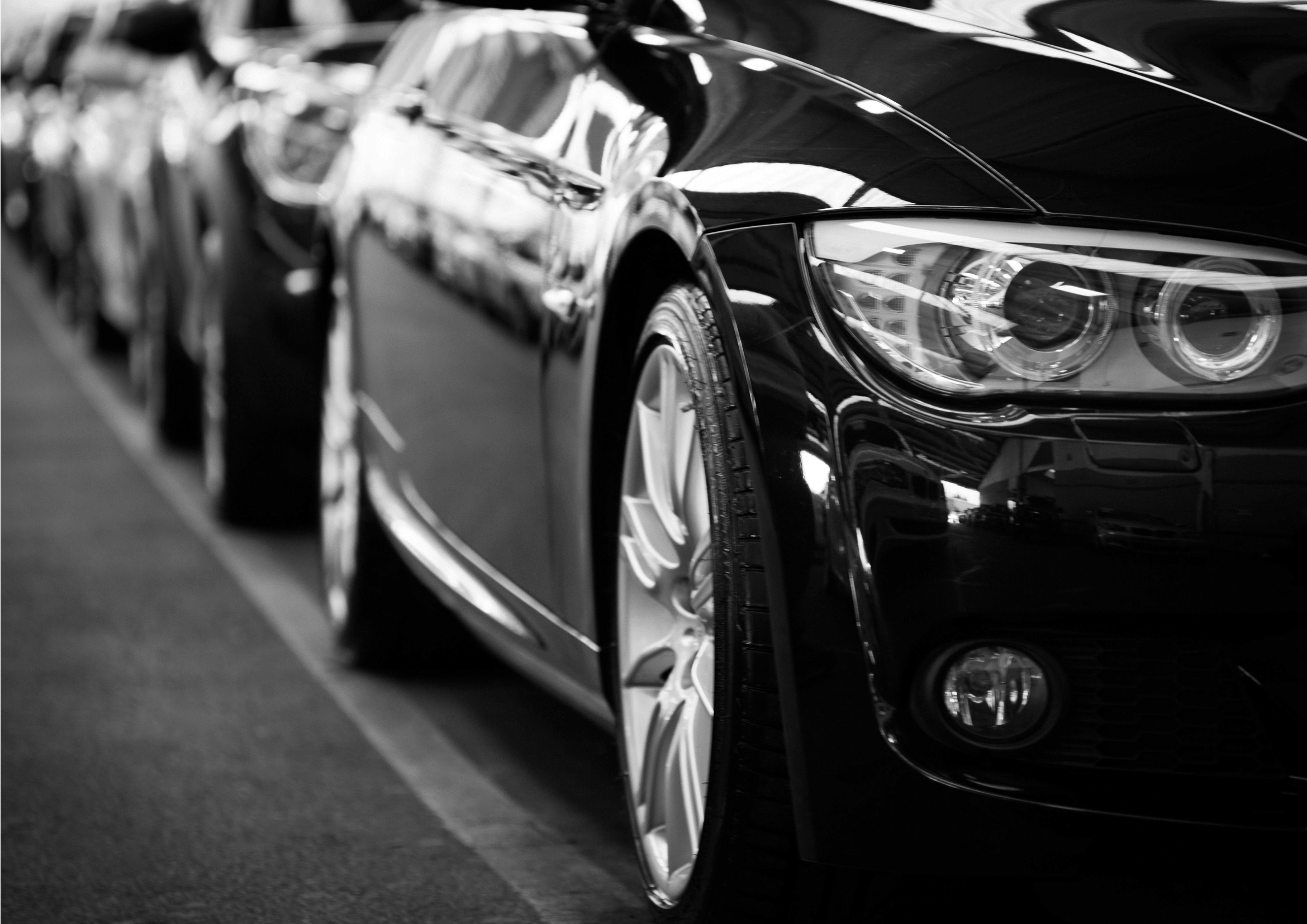
The Trade War Fallacy: Why the Steel Industry Needs Innovation, Not Protectionism
This month, President Donald Trump announced the imposition of a 25% tariff on all steel and aluminum imports to the United States, effective March 12, 2025. This policy aims to protect domestic industries from foreign competition accused of flooding the U.S. market with cheap steel and aluminum. The administration argues that these tariffs are necessary to safeguard national security and preserve American manufacturing jobs, arguing that this ensures a stable and secure supply chain. While this may seem to provide some short-term economic benefits, it ignores the dynamics that could enhance the industry, particularly in areas like sustainability and technological advancements. In contrast, we believe that the automotive steel industry’s future lies in regional integration, circularity, and innovative, sustainable production methods. The rationale for this perspective is clear:
From the earliest motor vehicles to today’s cutting-edge electric cars, steel’s versatility and strength have been crucial in shaping the evolution of the automobile industry. Steel has been the backbone of automotive evolution, shaping cars into the wonders cherished by drivers and enthusiasts everywhere.
Karl Benz’s three-wheeled vehicle, which appeared in 1886, had its chassis made of wood and its wheels of ironclad. Then Henry Ford introduced his Model T, putting steel at the heart of the automobile industry. The Model T’s steel frame provided unmatched durability and strength. By 1927, over 15 million Model Ts had been produced. Automotive steel’s impact on mass production and automotive design has suddenly become undeniable.
The next automotive boom came in the post-World War II era. Again, steel was at the forefront; steel’s robustness and malleability made it possible to manufacture millions of vehicles to meet the exploding demand for cars. This era was supported by new steel technologies, such as continuous casting, which improved the efficiency and quality of steel production.
In the 1980s, it became apparent that cars required lighter and more fuel-efficient materials. Reduced vehicle weight brought fuel efficiencies, translating into fewer emissions and smaller carbon footprints. Lightweight steels also enhance vehicle performance by improving acceleration, handling, and braking, while allowing a more enjoyable driving experience. During this period, we saw the introduction of high-strength steel alloys (HSLA). These innovative materials enabled vehicles to weigh about 25% less than those made with traditional steel. Following their introduction, HSLA steels quickly became the norm.
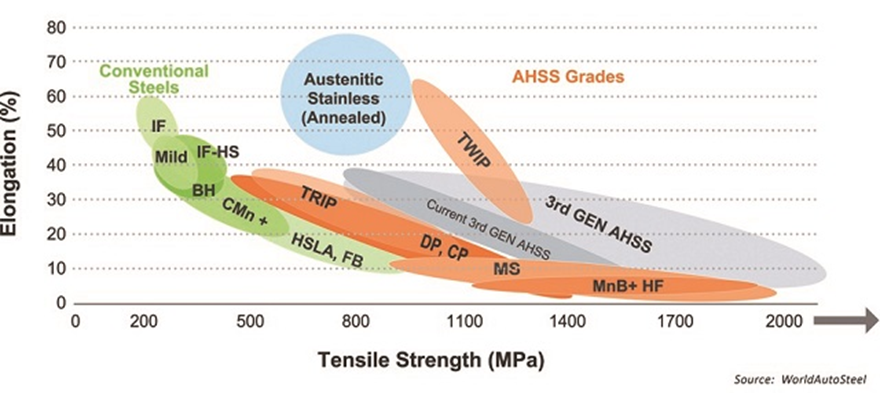
Recently, we have been witnessing the introduction of advanced high-strength steels (AHSS). As cars are built with these, they become even safer, more fuel-efficient, and environmentally friendly. As we entered 2020, AHSS were already seen to account for nearly 60% of the steel used in new cars, contributing to a 10% reduction in overall vehicle weight and a corresponding 6-8% improvement in fuel efficiency. In terms of safety, modern cars are designed with crumple zones made of high-strength steel, which can better absorb and dissipate energy during collisions, protecting the vehicle’s occupants. The strength of steel also ensures the integrity of the passenger compartment, reducing the risk of injury in accidents.
Innovations in metallurgy and steel manufacturing processes will continue to make this versatile material even stronger, and lighter and provide car makers with ever-increasing attractive properties. With the rise of electric and hybrid vehicles, the demand for lightweight materials has become even more pressing than ever.
In recent years, the sustainability aspects of steel production have gained significant scrutiny. The sustainability of car makers’ supply chains is also driving the demand for greener steel. “Green steel” is often understood to mean just steels produced by using renewable energy sources. However, truly eco-friendly steelmaking requires innovative processes that reduce CO2 emissions as well as other pollutants. These solutions are found in the adoption of more advanced electric arc furnaces (EAFs) or other modern technologies such as hydrogen-based reduction.
The energy source is just one aspect of the greener steel conversation. Steelmaking also comes with several other serious environmental and safety concerns. For instance, several potentially toxic metals and chemicals are inevitably part of the manufacturing and recycling processes. How modern steelmakers manage these metals and chemicals and how they recycle scrap steel will be key to their future viability and economic success. Circularity may also become the defining driver of both automotive steelmakers and their clients’ performance and value. How will end-of-life vehicles be recycled? How will the recovered steel be reused in new car production? Still, too little attention is given to these two concerns.
Steel’s journey from a heavy, bulky metal to a lightweight, high-strength material reflects the evolution of the cars themselves. Steel manufacturer’s adaptability and evolution will remain a cornerstone of automotive manufacturing.
As steel technology continues to evolve with a strong emphasis on reducing carbon footprints and incorporating recycling, regionalized production hubs that focus on recycling and reusing steel will likely become key. This strategy aligns with the growing demand for “green steel” and the circular economy, where scrap steel from end-of-life vehicles is recycled and reintegrated into the manufacturing process. By focusing on sustainability, car manufacturers and steel producers can create a more efficient, environmentally friendly, and resilient supply chain that reduces dependence on traditional, resource-intensive mining and imports. This vision of a more vertically integrated industry, with an emphasis on local recycling and green technologies, would not only lower costs in the long run but also bolster the sector’s adaptability and future-proof it against the rising environmental and regulatory demands of the global market.
The trade war over steel tariffs is misguided because the real focus should be on creating a more integrated, sustainable steel production system that works hand-in-hand with the automotive industry. Rather than imposing tariffs, efforts should be directed toward advancing the development of high-quality, eco-friendly steel, promoting regional recycling, and creating a circular economy that supports both the steel and automotive sectors in a more efficient and future-proof way.
Post a Comment
You must be logged in to post a comment.